2022年6月号
グループ企業探訪
AM(Additive Manufacturing)市場を牽引するAMソリューション専業会社
NTTデータ ザムテクノロジーズは、産業用3Dプリンタの販売、保守、ならびに材料の開発、販売、3Dプリンタに適した設計支援・コンサルティングから製造受託まで提供する、AM(Additive Manufacturing)ソリューション専業の会社だ。AM関連分野は新しい市場で今後の伸びが期待される中、業界のリーディングカンパニーとして今後の市場拡大を牽引するための適用領域拡大、設計等データ流通プラットフォーム、新たなサプライチェーンのコンセプト等を展開していく思いを水沼憲一社長に伺った。
NTTデータ ザムテクノロジーズ 水沼憲一社長
ものづくりのデジタル化を体現するAM技術のソリューション
◆設立の背景と目的、事業概要について教えてください。
NTTデータ ザムテクノロジーズ(XAM:ザム)は、1977年に設立された日立造船情報システム株式会社の事業を2006年に引継いだNTTデータエンジニアリングシステムズから、AM(Additive Manufacturing)に関する事業を分離独立して2020年5月18日に設立されました。
昨今、ものづくりの技術はコンピュータ数値計算により3次元設計技術が高度化し、製品性能の発揮に最適な機能形状を設計することが可能になりました。一方、あまりに複雑な形状は、従来の工法では製造が困難であることが大きな課題となってきました。こうした中、AM技術の進歩により、非常に複雑な形状を適切な品質基準を満たしたうえで造形する3Dプリンタが登場してきました。XAMは、グローバル市場における3DプリンタによるAM技術の進展と関連マーケットの拡大を背景に、AMというマーケットに対して、当社の持つAM技術とNTTデータグループのIT/AI(人工知能)技術を融合させることで、飛躍的な事業発展につなげることを目的に、AMソリューション専業の事業会社として設立され、2020年7月1日より事業を開始しました。
XAMは、インダストリアル3DプリンタのグローバルトップシェアのドイツEOS社の販売代理店として、3Dプリンタの販売、保守などのトータルソリューションを行うだけではなく、自らが3Dプリンタを所有して部品製造を行う製造受託を行っています。
この製造受託では、受託により部品を製造するだけではなく、自らが培った製造ノウハウをコンサルティングサービスとして提供することにより、これまでのEOSの販売代理店の枠組みにとどまらず、AM技術の活用促進に向けた活動に注力しています。国内AM市場を活性化させ、お客さまとともにAMの成功を導き出すことで、AMの事業拡大を図っています。
◆AM技術とはどのような技術でしょうか。
AM技術は積層造形技術とも呼ばれ、積層的に材料を積みあげながら3次元形状を作成する技術の総称です。AMにはいくつかの方式がありますが、その中でもっともシェアが高く、当社でも取り扱っているLPBF方式では、土台となる平板の上に材料となる金属や樹脂の微小な粉末を均一に敷き詰め、そこにレーザ光を照射することで粉末を溶解し、固めます。レーザ光は製造する造形物を薄く輪切りにした形状を数値化した設計データに基づいて照射されます。これを何層にもわたって繰り返していくことで、最終的な造形物が出来上がります(図1)。
これまで、エンジンの部品等の複雑な形状をしたものは、複数の部品を組み合わせてつくり上げる、もしくは複数の鋳造部品を溶接等によりつなぎ合わせることでつくり上げられます。AM技術により、これらの造形物は一体成型によりつくることが可能になり、接合なく一体でつくることにより堅牢になり耐久性が向上するばかりではなく、部品数の削減、金型が不要であることからリードタイムの短縮が可能といった特長があります。
完成品の品質は、3Dプリンタの機能・性能および動作に依存し、3Dプリンタの動作は設計データに依存するため、設計データの精度・品質が重要なファクタとなります。XAMには、部品の形を決める際に体積、質量、剛性、振動特性といった要件を考慮しながらもっとも適した形状を策定する「トポロジー最適化」の技術と、人手による設計では不可能な複雑で高機能・高性能な形状をコンピュータの支援で設計する「コンピュテーショナルデザイン」の技術、そしてこれらの活用ノウハウが蓄積されており、ビジネス上の大きなアドバンテージとなっています。
AM技術・品質の認知度向上と適合領域拡大で市場拡大をめざす
◆AM技術による造形はまだ新しいビジネス分野のようですが、どのような事例があるのでしょうか。また、市場はどのような状況にあるのでしょうか。
実は「AMは20年以上歴史のある技術」であり、過去にはメイカーズが出版されるなどのブームもありましたが、まだまだ製造業の一部に限定されており、そういった意味では、まだ新しいビジネス分野といえるかもしれません。
AM技術はその特長から、少量多品種の製造に向いています。その代表的な事例として、三菱重工業株式会社様と連携した、宇宙航空研究開発機構(JAXA)様向けのH3ロケット用LE-9エンジン部品の提供があります(図2)。ロケットのエンジンには非常に複雑な形をした部品や、複雑な形に曲がった配管が多数使われています。こうした部品を3Dプリンタで製造することで、インジェクタという部品の場合、一体成型によりリードタイムが大きく短縮され、堅牢化、部品数削減に寄与できます。例えば従来であれば約500点の部品が必要なところ、1つの部品として製造することができました。また、配管についても従来の曲げ加工による成型と比較して、曲げ部の金属の肉厚のバラつきを少なくすることが可能となりました。
AMの市場は、グローバル市場が先行しており、年間成長率が15〜20%で、2022年には1兆6000億円を超えるといわれています。このうち、金属AMと樹脂AMはおよそ1対2の比率ですが金属AMの比率が増えています。これと比べて日本の製造業では厳格な品質管理基準があり、AMのような新しい工法に対して、まだ品質管理手法が確立されていないため日本国内のAM市場はまだ立ち上がっていない状況です。金属AMの市場においては、2022年の予測値として日本の市場規模はグローバルの20%にも届いていない状況ですが、当社は、その品質管理手法をロケット開発の中で磨き上げ、スタンダード化することにより、市場の拡大が期待されます。その中で現在XAMは約30%のシェアを担っています。
AM技術は複雑形状、オーダメイド、試作等の少量生産などの領域において積極的に活用が進んでいます、現段階では、効率、コストの面ですべての部品製造に適しているとはいい難い状況です。今後技術革新が進むことで、このような課題は減少していくと想定していますが、こういった背景からAM技術により製造される製品は、主に航空、宇宙、医療(主として歯科のインプラント)の業界で利用されています。グローバルにおいてはこれらの業界がAM技術の市場を牽引していますが、日本においてはこれらの業界そのものの規模が小さく、製品が浸透しづらい環境にあります。また、国内の製造業は高い技術力のベースがあり、AM技術に整合性がある製品でも既存技術である程度対応できてしまい、新市場へのシフトが進まないといった点等が、日本市場の出遅れの原因になっていると考えます。
◆今後の展望についてお聞かせください。
AMは進化を続ける技術で、IT/AI活用の強化によるQCDの向上や、いち早く先進技術を取り入れるための海外企業アライアンスなどを活用していきます。これらの取り組みと当社が持っているAM技術のコラボレーションにより事業規模を現在の20〜30億円から2025年には100億円をめざします。
AM技術により、在庫、リードタイム、物流といったサプライチェーンの概念が全く変わってきます。①一体成型による部品数削減、②オンデマンド生産による在庫レス、③3Dプリンタによりあらゆるものの製造が可能になることによる最適化生産が可能となりますが、私たちXAMでは、今後、設計データや製造ノウハウなどを蓄積・プラットフォーム化し、日本のものづくりの緻密なノウハウをAM技術におけるデジタルQMSとしてプロセス確立(ソフトウェアによるアセット化)を進め、日本独自の付加価値を競争優位の源泉としてグローバル市場におけるサプライチェーンに取り組んでいきます。
担当者に聞く
困難な製品内部状態の品質管理にデジタルでチャレンジ
技術開発統括部 統括部長
酒井 仁史 CTO
◆担当されている業務について教えてください。
製造装置である3Dプリンタを含めてAM技術は依然コストが高いため、コストに見合う付加価値を生み出すことができる活用領域を見つけ、それに合った製品の開発、量産から品質保証までのプロセス構築を行っています。通常、お客さまがAM技術による製造装置を購入して利用する場合、お客さまのつくりたい製品が必ずしもAM技術に適したものではありません。そこで、技術的リスク、経済的リスクを評価し、3Dプリンタの導入から、製造設計、量産、運用、品質保証までの一連のプロセスを構築しお客さまをサポートしています。こういったかたちでエンジニアリングを行っている会社は、日本にはあまり存在していないので、そこが私たちの出番です。
最近取り組んでいる事例としては、熱交換器(ヒートシンク)に関するもので、現在注目されている領域の1つです。熱交換器にはいろいろな仕組みのものがありますが、伝熱面積(表面積)を多くとって、熱交換性能を上げるというのが基本原理です。ただ、そこに着目しすぎると、構造が複雑になり、製造が困難になると同時に、圧力損失が大きくなり(冷却のための空気等の流れが悪くなり)、逆に熱がこもってしまいます。私たちはこの熱交換性能と圧力損失の二律相反する関係の最適解を見つけつつ設計をしています。
通常の製造工程では、鋳造等による部品を組み合わせてつくるため、製造工程、成型における限界も考慮して設計する必要があり、必ずしも最適解を持った製品ができるわけではありません。一方で、AM技術による製造では、基本的には複雑な構造を持った製品でも自由につくることができ、使用する設計データはすべてデジタル化されたものなので、コンピュータ上でシミュレーションを行いながら、結果を設計データにフィードバックしていくことで、最適解の熱交換器に関する設計から製造まで一貫したプロセスが出来上がります。鋳型をつくる必要もないので、必要に応じて試作して実験することも可能になります。
◆課題を伺えますか。
コストと品質が大きな課題だと考えています。
自由度が高いとはいえ、AM技術は結局ものづくり、部品づくりの技術です。したがって経済合理性が確立しない限り普及は困難です。現在のAM技術関連コストは高く、このままでは普及にブレーキがかかってしまいます。将来的な技術革新でコストが下がることは期待できますが、少なくとも現段階においては、航空事業、医療、モータースポーツのように、高品質が要求されて、かつ少量生産で高付加価値なものづくりの領域では経済合理性が確立されているので、この領域のビジネスに注力しています。
品質については、AM技術は粉末をレーザ照射により溶解し固めるという原理であり、これはまさにバーナー等で金属を溶かして固めることで接着する溶接と同じ技術です。一般的に溶接面は外から確認できないため、品質検査においてはCTスキャンやX線等による非破壊検査が行われるのですが、コストがかかることもあり、品質検査・保証が難しいといわれています。AM技術も溶接の一種である以上、同様な問題が内在しています。しかし、AM技術による製造過程で、センサを設置することで、レーザ照射付近の酸素濃度、レーザの出力、照射角度、粉末の材質、溶解した粉末の形状、固まるプロセス等のデータを収集し、蓄積することが可能です。こうしたデジタルデータと非破壊検査等で得られた結果を対比させ、解析することで、製造過程において品質検査が可能になります。逆に、製造装置の各種設定値を、高品質の状態のデータに合わせることで、常に安定した品質の製品を製造することも可能になります。現在、こうしたデータを収集・蓄積しているところであり、より多くのデータを収集・蓄積することで検査の精度を上げていくつもりです。
◆今後の展望について教えてください。
技術の責任者として、前述のような課題解決を進めていくことで、AM技術をより洗練されたものとしていくとともに、導入、設計から製造、品質管理までのプロセスに関する知見を蓄積して、広くお客さまに展開していくことをめざしています。
また、レーザの利用といった既存の技術にとらわれずに、新しい技術、プロセスを積極的に取り入れていくことで、AM技術の適用領域をさらに広げていきたいと考えています。
ア・ラ・カルト
■XAMの工場
デジタル制御された3Dプリンタというと、オフィス内に設置されたプリンタを想像してしまうのですが、XAMには3Dプリンタが設置された工場が2つあります。縦・横・高さが最大40cmのものをつくる装置は、なんと縦・横・高さが4.2m×1.6m×2.4m、重さが4.8tもあり、とてもオフィスに入るようなものではありません(写真1)。元々はラボとして出発した工場なのですが、お客さまのニーズが高まるにつれて装置の数も増えて、現在では合計で13台の装置が設置されているそうです。
■新工場、Digital Manufacturing Center(DMC)オープン
2022年7月オープンに向けて新工場をつくっています。建物はすでに完成し、今は装置やオフィス家具の搬入設置等を行いながらオープンを待つ状況です(写真2〜4)。ニーズの高まりを視野に入れて、手狭になった既存工場の2倍くらいの数の装置が入る広さに、縦・横・高さが各1mの製品製造に対応できる装置や、センサからのデータによる品質管理システムと生産管理システム、製造実行制御システムとが連携した環境を整え、残存している人手による工程も自動化していくそうです。こうした新しい取り組みにチャレンジしているところを、ショールームとして展示し、可視化された各プロセスをベースに、お客さまとディスカッションすることで共創していく場としたいとのことです。
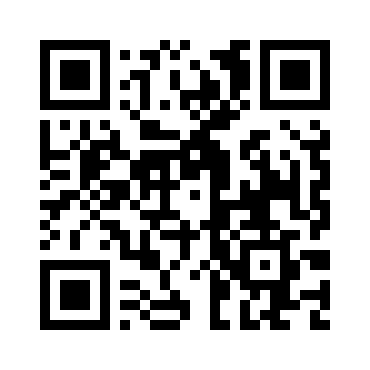